Ohe Mill
Ohe Mill, completed on the western waterfront of Kawanoe in 1979 with a site area of 460,000m2 is equipped with chemical and mechanical KP (kraft pulp), TMP (thermomechanical pulp), and CTMP (chemical thermomechanical pulp) virgin pulp and DIP recycled pulp manufacturing facilities that produce paper for newsprint, publishing/printing, hygiene products, and more.
Taking advantage of our coastal location, we transport raw materials and fuel such as woodchips and coal to Ohe Mill via a conveyer belt directly from cargo ships docked at the port located to the east of the plant. Then almost half of all finished products are shipped out from the port located to the west to mainly Kanto, Kansai, Chugoku, and Kyushu regions. This is one of the aspects that gives our company an edge.
- Ohe Mill in 1980
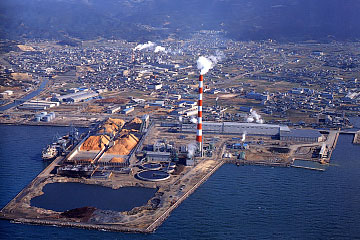
- Ohe Mill today
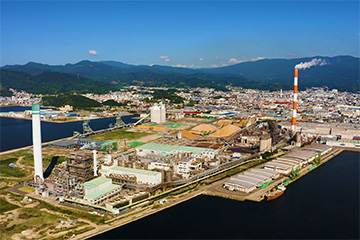
Technology that protects the environment
Effective use of wastes
We always concern about wastes. With the aim of "Zero discharge" mill, at first, we try to reduce the fiber and filler loss from papermaking process. Paper sludge from the effluent treatment facilities is utilized as an energy resource at incinerator and also recovers an energy simultaneously. Incinerated fry ash from both coal and sludge boiler can be effectively used as a raw material for cement industries and also used for engineering material.Ash recycle plant was built in 2018,some of the ash are used for soil improvement agent.
- Sludge Boiler
- Fly Ash Silo
CO₂ reduction
Recovery Boiler
We are also taking measures for energy conservation as a step toward CO₂ reduction, and we have implemented highly efficient energy utilization system, shifted to pulp production with low energy consumption, along with the collection of exhaust heat and the installing of highly efficient equipment. Moreover, we work to prevent global warming by promoting the use of biomass fuel,tire chip and RPF as well as reducing the use of fossil fuel. Consequently, we have already accomplished the goal of Japan Paper Association.
( RPF : Refuse derived paper and plastics densified Fuel )
Water quality control
Water use in each process is effectively controlled by a closed system, and waste water is reduced at each stage for example. As a result, we are able to operate factories with a low level of basic units of waste water and COD. Moreover, we work on reduction of further waste water in our new KP plant, through waste water treatment technological research. To preserve the environment of the Seto-Inland Sea, we have been endless efforts for contributing to water quality of the Seto Inland Sea.
- Waste Water Treatment Facilities at Ohe Mill
- Waste Water Treatment Facilities at Ohe Mill
Creative technologies –it all begins with high-quality materials–
High quality pulp from cutting edge technology and a concern for the environment.
Fiberline(Digester)
Marusumi provides the integrated production system ranging from pulping and, papermaking and finishing. For pulping, we produce three kind of pulps i.e. Kraft pulp, Deinked pulp and mechanical pulp In June, 2007, we built a state-of-the-art Fiberline taking environment friendly and energy conservation. We also produce high quality and high yield pulp.
DIP,Drum Pulper and High Consistency Pulper
- CTMP(Chemi-Thermo Mechanical Pulp),Primary Refiner
- Fiberline(Bleaching Tower(ECF))
- DIP,Flotater
- Pulp Sheet Machine
Creative technologies -Paper Machines-
World's largest newsprint paper machine with leading-edge-performance
Ohe Mill has paper machine No1 and No2 the world's largest class of newsprint paper machines. The advanced technologies enhance the papermaking process by producing newsprint in 8,130mm width. The machine, equipped with the latest soft nip calender corresponding to weight saving and color printing of newsprint, allows us to produce paper products with good printability including ink set and reproducibility.
Paper Machine No.2,Ohe Mill Paper Machine No.1,Ohe Mill
Papermaking machine using pulp manufactured in-house to produce high quality hygienic paper
The No.4 papermaking machine at Ohe Mill uses pulp made at Ohe Mill to produce safe, high-quality hygienic paper including paper towel, kitchen and tissue papers usable as food contact material or hand towels.
Mill Facilities , Ohe Mill
Pulping Plants
Ohe Mill
Facilities |
Number |
Production capacity
(ton/month) |
Kraft Pulp(KP) |
1 |
21,000 |
Thermo Mechanical Pulp(TMP) |
3 |
13,500 |
Chemical Thermo Mechanical Pulp(CTMP) |
3 |
15,000 |
Deinked Pulp(DIP) |
3 |
21,000 |
Pulper |
1 |
12,000 |
Power Plants
Ohe Mill
Facilities |
Number |
Capacity |
Coal boiler |
3 |
538 tons/hour |
Recovery boiler |
1 |
179 tons/hour |
Oil boiler |
1 |
170 tons/hour |
Oil boiler (reserve) |
3 |
81 tons/hour |
Sludge boiler |
2 |
90 tons/hour |
Bark dust boiler |
1 |
32 tons/hour |
Steam turbine |
6 |
175,900 kw |
Water and gas treatment equipments
Ohe Mill
Facilities |
Number |
Capacity |
Waste water
treatment |
Coagulating sedimentation |
2 |
195,900㎥/day |
Activated sludge |
2 |
185,500㎥/day |
Screw press |
16 |
6,040㎥/day |
Flue gas
treatment |
Flue gas desulfurizer |
7 |
1,110,000N㎥/hour |
Dust collector |
9 |
1,350,000N㎥/hour |
Odor gas
treatment |
Deodorization device |
1 |
liquid70tons/hour gas8,000N㎥/hour |
Paper Machines
Ohe Mill
Paper Manufacturing
Equipment Model |
Width
(mm) |
Capacity
(ton/month) |
Products |
#1 Twin Wire
(with size press) |
8,130 |
16,500 |
Newsprint,telephone
directory paper,
publication paper,
Hygienic paper |
#2 Twin Wire
(with size press) |
8,130 |
18,000 |
Newsprint |
#4 Yankee cylinder |
3,520 |
2,700 |
Hygienic paper |
Soil stabilizing agent manufacturing
Facility |
Number |
Capacity |
Soil stabilizing agent manufacturing |
1 |
11.75tons / hour |
CNF pilot plant
Facility |
Capacity |
CNF pilot plant |
50tons / year |